對于厚度僅 0.8mm 甚至 0.1mm 的超薄工件,焊接過程的溫度與時間控制直接決定焊接質(zhì)量與工件完整性。超高頻焊接機憑借 “微區(qū)加熱、瞬時響應(yīng)” 的特性,成為超薄工件焊接的理想選擇,既能實現(xiàn)完美熔合,又能避免工件因過熱而損傷。
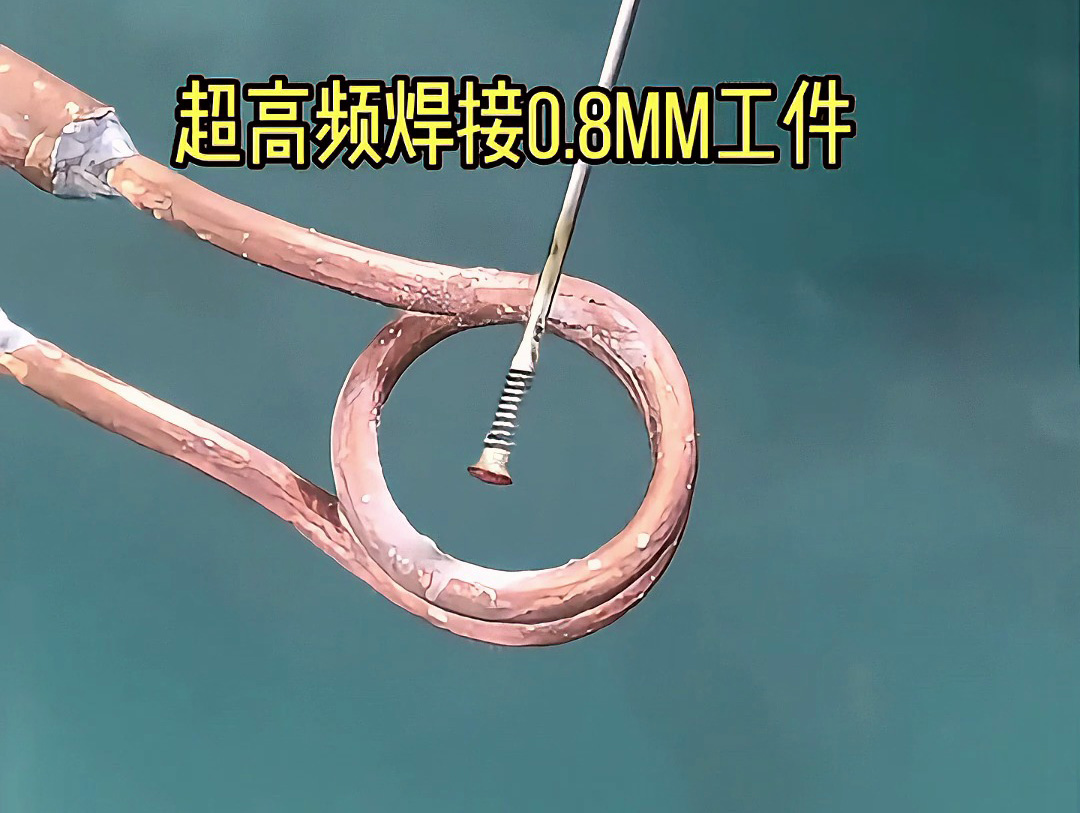
針對 0.8mm 厚度的工件(如精密電子元件的銅片、不銹鋼薄片),超高頻焊接機(頻率通常 200-400kHz)的精細控制能力凸顯:
溫度精準可控:通過高頻交變磁場(趨膚效應(yīng)極強),將熱量嚴格限制在焊接接口處,加熱溫度可精確控制在焊料熔點 ±5℃范圍內(nèi)(如焊接 0.8mm 銅片采用錫鉛焊料時,溫度穩(wěn)定在 183-190℃),避免工件因溫度過高導(dǎo)致的變形或性能退化;
時間微秒級調(diào)節(jié):完成 0.8mm 工件的焊接僅需 0.5-2 秒,超短加熱時間減少熱傳導(dǎo)對非焊接區(qū)域的影響,工件整體溫升≤30℃,尤其適合對熱敏感的電子元件或精密結(jié)構(gòu)件;
焊縫均勻美觀:超高頻的能量聚焦使焊料熔融充分且分布均勻,焊縫寬度可控制在 0.3-0.5mm,無傳統(tǒng)焊接的 “溢料”“虛焊” 問題,力學(xué)性能檢測顯示,0.8mm 不銹鋼薄片焊接后的抗拉強度可達母材的 85% 以上。
某精密儀器廠的應(yīng)用案例顯示,采用超高頻焊接機處理 0.8mm 銅質(zhì)接線端子后,焊接合格率從傳統(tǒng)高頻焊接的 82% 提升至 99.5%,且因過熱導(dǎo)致的端子氧化率幾乎為零。
超高頻焊接機的技術(shù)優(yōu)勢在 0.1mm 工件(如箔片、微型傳感器電極)焊接中更具顛覆性:
微區(qū)能量聚焦:采用定制化微型感應(yīng)線圈(直徑可小至 0.5mm),將磁場能量集中于直徑≤1mm 的焊接點,實現(xiàn) “點對點” 加熱,0.1mm 鋁箔焊接時,非焊接區(qū)域溫度僅上升 10-15℃,完全避免材料脆化;
動態(tài)響應(yīng)速度:設(shè)備功率調(diào)節(jié)響應(yīng)時間≤10 微秒,可根據(jù)焊料熔融狀態(tài)實時調(diào)整能量輸出,防止 0.1mm 工件因瞬間過熱而燒穿(傳統(tǒng)焊接機因響應(yīng)慢,0.1mm 工件燒穿率高達 30%,超高頻焊接可降至 0.5% 以下);
工藝適配性廣:無論是金屬箔片的搭接、異種材料(銅 - 鎳、鋁 - 銅)的微連接,還是微型元件的密封焊接,超高頻設(shè)備都能通過參數(shù)微調(diào)(如 0.1mm 鎳箔焊接采用 150kHz 頻率、0.3 秒加熱時間)實現(xiàn)穩(wěn)定連接。
這類超精細焊接技術(shù)廣泛應(yīng)用于高精密領(lǐng)域:
醫(yī)療器械中的微型導(dǎo)管焊接;
航空航天的箔式傳感器連接;
電子芯片的引線鍵合預(yù)處理。
操作時需注意:
線圈與工件的間距需精確控制在 0.1-0.2mm,確保能量聚焦;
采用惰性氣體保護(如氬氣),防止 0.1-0.8mm 工件焊接時產(chǎn)生氧化;
定期校準設(shè)備的功率與時間參數(shù)(每月 1 次),保證微米級焊接的一致性。
超高頻焊接機通過對溫度與時間的極致控制,突破了超薄工件焊接的技術(shù)瓶頸,既滿足了 0.8mm 工件的精細焊接需求,又實現(xiàn)了 0.1mm 工件的穩(wěn)定連接,為高精密制造領(lǐng)域提供了可靠的超微焊接解決方案。若您有超薄工件的焊接需求,可根據(jù)材料、結(jié)構(gòu)定制專屬焊接參數(shù),歡迎咨詢技術(shù)細節(jié)。